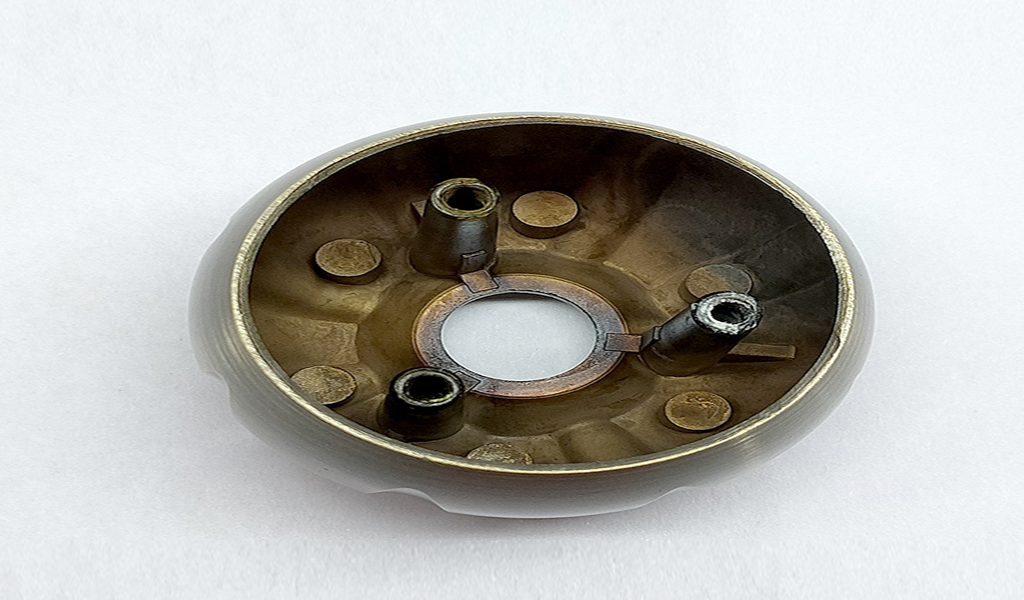
1. Control of the production process of stamping parts
1. Determine the process plan
When determining the process plan of stamping parts, the nature of the stamping process can be determined through the part drawing. Reasonable arrangements can improve production efficiency and product forming time.
2. Improve the mold installation process
The correct mold can prolong the service life of the mold. If the mold design is not perfect, the subsequent fabrication of the stamping parts will not be realized, resulting in quality problems of the stamping parts.
3. Clarify the stamping direction
When determining the stamping direction, one is to ensure that the punch can enter the concave die, and the other is to consider whether the feeding resistance of each part of the pressing surface is uniform and reliable. The reasonable shape of the binder surface and the blank binder force make the resistance of each part of the binder surface even and moderate, reduce the drawing depth, open process holes and process incisions, etc. The surface quality of the stamping parts is generally not damaged during stamping, and the stamping has good interchangeability and has the characteristics of “exactly the same”.
2. Control of the fabrication technology of automobile stamping parts
1. Drawing process
The first step in the stamping process is the stretching process, and the quality of the stretching process lays a good foundation for trimming and flanging. The binder has a certain drawing effect on the drawn blank, but if the number of wrinkles generated in the drawing process is small, it may be eliminated by the drawing effect, so it is difficult to make a more accurate judgment on the formed wrinkles.
2. Wrinkle control
The main reasons for the drawing process of the drawing parts are as follows: the sheet metal flows too fast during the feeding process of the stamping parts, forming wrinkles; Wrinkling is formed quickly; the mold positioning design is unreasonable, which leads to the inability to press the material during the drawing process of the stamping part or the pressing edge is too small, resulting in wrinkling; the gap between the convex and concave dies is too large to cause wrinkling.
3. Process management
Sometimes it is scrapped due to surface defects of the blank. Use the plate type corresponding to the process to avoid stress deformation caused by the performance of the plate. Surface flaw detection is also required after forming. For curved tensile parts with complex shapes, the radial tensile stress should be increased to control wrinkling; The high-end special stamping oil can effectively avoid cracking, burr and other problems of stamping parts through the release of extreme pressure agent during the stamping process, and can greatly improve the surface finish of the workpiece and the production and fabrication efficiency.
3. Stamping quality control
The quality control of stamping forming is to make real-time adjustments through the prediction and monitoring process of statistical control methods, thereby improving production efficiency and production benefits.
1. Arrangement diagram method
The purpose of drawing an arrangement diagram is to visually represent it in a graphical way, so that the manufacturer can clearly identify where to start to improve product quality.
2. Control chart method
The control chart is based on the application of statistical technology to realize process control. It is mainly to trace points in time for each process in the dynamic production process according to certain rules to obtain control charts, and take measures to reduce costs.
4, increase the detection technology
The inspection of stamping parts is an important means to avoid batch problems of stamping parts. The second is the matching size detection. The measurement content must be analyzed in combination with the specific part situation. Correct adjustment will achieve good results. The next step is to improve the quality of testing personnel, to avoid rushing for success, and mass production can only be done after all the inspections are qualified.
In a word, in order to control the quality of automobile stamping parts, it is necessary to comprehensively manage various factors that affect its quality. Different manufacturing and production methods lead to different management methods and means. Through the production of these four steps, a qualified automotive stamping part is born.
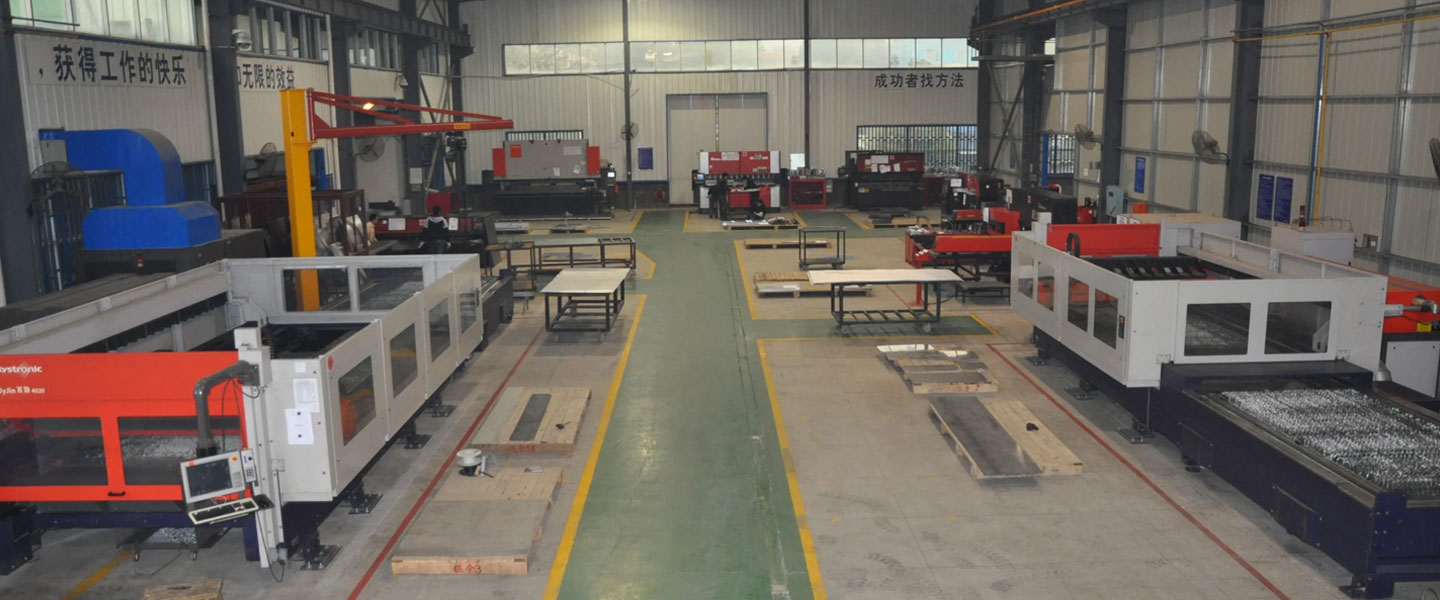
Pintejin Sheet Metal shop offers a cost-effective solution for a wide range of industries with our custom metal stamping and custom sheet metal fabrication capabilities. Our stampnig operations include a variety of sheet-metal forming manufacturing processes, such as punching, blanking, embossing, bending, flanging, and coining. Our professional, experienced and well-trained engineers can execute the complex metal stamping operations with precision and accuracy.
No matter what your metal fabrication needs are, Pintejin can offer the right solution: from single sheet metal part or sub-assembly of stamped metal parts to turnkey solutions for mechanical and electrical assemblies. We have the technology, equipment and the experience to fabricate customised metal products from aluminium sheet metal fabrication, steel, zinc plated steel, stainless steel sheet metal fabrication, brass and copper. Designs that require CNC machining of surfaces or components can be accommodated. We can supply polished, galvanized, zinc coated or powder coated finishes for any sheet metal work or stamped metal components. Coupled with our accurate and reliable metal fabricating equipment, we guarantee precision and repeatability in custom sheet metal work. You’ll be taking advantage of the best sheet metal fabrication china can produce.