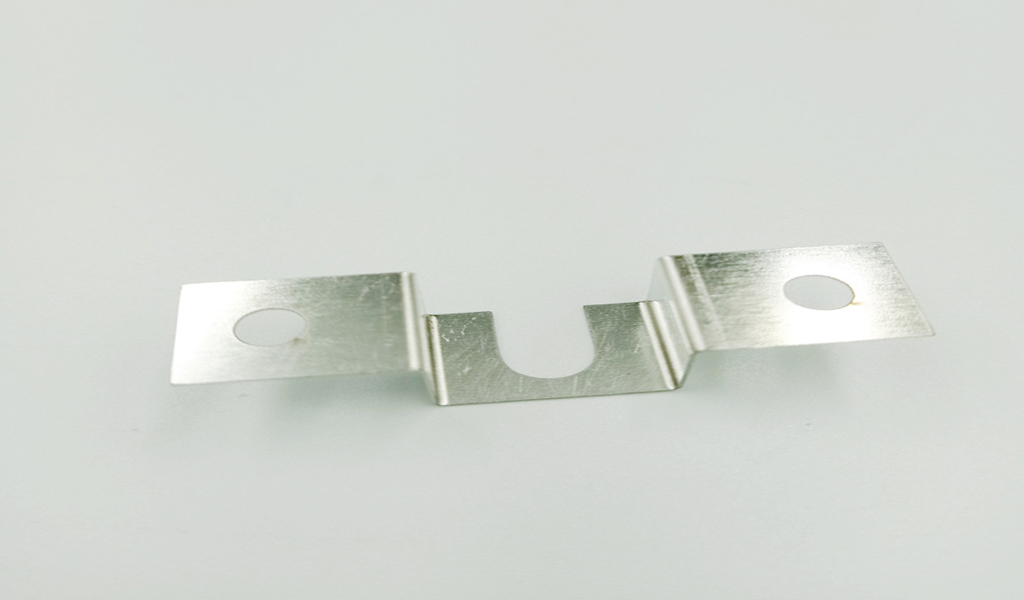
In the process of using stamping parts, there will be bad phenomena, so what is the cause of this bad phenomenon?
- 1. Sheet material: The coil material is damaged or the edge is wrinkled, and the wrinkling phenomenon that occurs when the gap between the guide rollers of the uncoiler line or the guide rollers on the mold is small, caused by the unbalanced feeding of the coil material; the burrs on the lower part of the cut surface of the steel plate, to When the burr height is 0.2 mm or more based on the cut surface, the iron powder generated here will damage the mold and cause unevenness.
- 2. The inner quality of the mold: the operator does not pay attention to the operation during the stamping process, the workpiece is displaced to the mold or collides with the corner of the conveyor belt when feeding and discharging materials; the conveyor belt height adjustment is unreasonable; the automation equipment adjustment is unreasonable (stroke, speed, etc. ). The problem that often occurs on the surface in stamping production is the concave and convex problem, which is mostly caused by the adhesion of dust or iron filings on the surface of the material or the mold, which reduces the surface quality of the workpiece and also reduces the productivity.
- 3. Coil material: foreign matter is mixed on the surface or inside of the steel plate; scratches (caused by the surface of the roller or foreign matter); roller traces (caused by foreign matter attached to the roller); foreign matter causes obvious groove marks on the surface depth.
What are the reasons for unilateral burrs in automotive stamping parts:
- 1. Mold assembly error. If the punch and the fixed plate are not perpendicular or loose due to wear, or because the positioning pin is loose, the correct fixed position of the convex and concave dies cannot be guaranteed.
- 2. Poor guidance accuracy. Excessive matching clearance of the die guides causes the centerlines of the upper and lower dies to not coincide, which affects the uniformity of the punching gap.
- 3. Installation error. When the unguided mold is installed, the position of the upper and lower molds is not allowed to cause uneven gaps. The surface of the upper platen or bottom plate of the mold is not clean, or the upper mold screw is not properly tightened, which will cause the working part to tilt.
- 4. The mold is deformed when working. For example, the leakage hole of the punching bed plate is too large, the lower template of the die is too thin, and the rigidity of the die is not enough, etc., the gap is affected by the deformation of the die during stamping.
- 5. The clearance between the guide rails of the punch press is too large, the parallelism between the bottom surface of the slider and the worktable is not good, or the sliding direction of the slider is not perpendicular to the worktable.
- 6. When the maximum resistance of the workpiece during punching exceeds 80% of the nominal pressure of the punch, it is easy to deform the “C”-shaped bed for an open punch, so that the center lines of the upper and lower dies do not coincide.
- 7. The flatness of the sheet is poor. During the metal stamping process, the punch with a smaller diameter is inclined.
- 8. Due to improper die material selection, forging and heat treatment process, the die is deformed during heat treatment or wire EDM, which affects the uniformity of die gap.
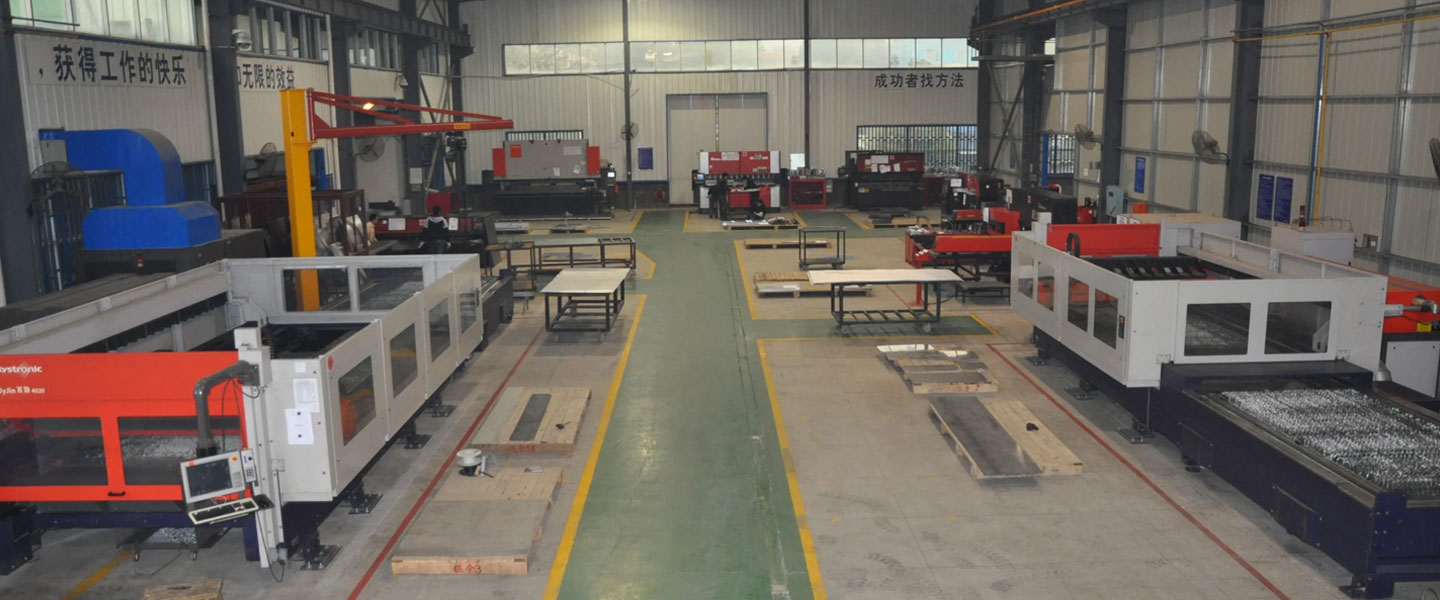
Pintejin Sheet Metal shop offers a cost-effective solution for a wide range of industries with our custom metal stamping and custom sheet metal fabrication capabilities. Our stampnig operations include a variety of sheet-metal forming manufacturing processes, such as punching, blanking, embossing, bending, flanging, and coining. Our professional, experienced and well-trained engineers can execute the complex metal stamping operations with precision and accuracy.
No matter what your metal fabrication needs are, Pintejin can offer the right solution: from single sheet metal part or sub-assembly of stamped metal parts to turnkey solutions for mechanical and electrical assemblies. We have the technology, equipment and the experience to fabricate customised metal products from aluminium sheet metal fabrication, steel, zinc plated steel, stainless steel sheet metal fabrication, brass and copper. Designs that require CNC machining of surfaces or components can be accommodated. We can supply polished, galvanized, zinc coated or powder coated finishes for any sheet metal work or stamped metal components. Coupled with our accurate and reliable metal fabricating equipment, we guarantee precision and repeatability in custom sheet metal work. You’ll be taking advantage of the best sheet metal fabrication china can produce.