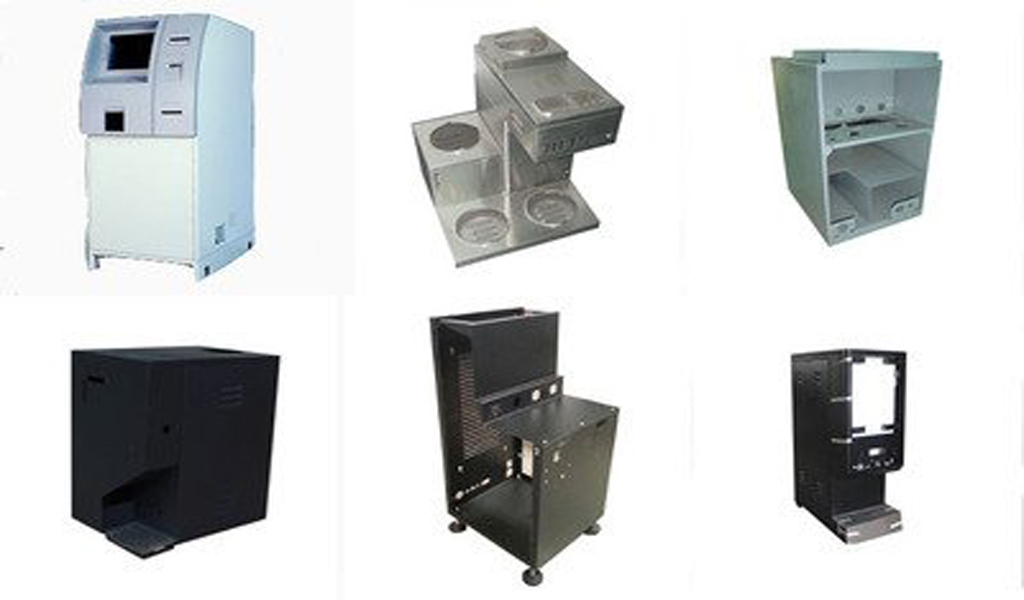
The stamping process can be roughly divided into two categories: separation process and forming process (also divided into bending, deep drawing, and forming). The separation process is to separate the stamping part and the blank from each other along a certain contour line during the stamping process, and the quality of the separated section of the automobile stamping part must also meet certain requirements; the forming process is to make the stamping blank plastic deformation under the condition of no damage , and converted into the required finished shape, and should also meet the requirements of dimensional tolerance and other aspects.
According to the temperature during stamping, there are two methods: cold stamping and hot stamping. This depends on the strength, plasticity, thickness, degree of deformation and equipment capacity of the material, etc., and the original heat treatment state and end-use conditions of the material should be considered.
The fabrication of cold stamped metal at room temperature is generally suitable for blanks with a thickness of less than 4mm. The advantages are that no heating, no oxide skin, good surface quality, convenient operation and low cost. The disadvantage is that there is work hardening, and in severe cases, the metal loses its ability to further deform. Cold stamping requires that the thickness of the blank is uniform, the fluctuation range is small, and the surface is smooth, spotless, and scratch-free.
Hot stamping is a stamping method in which metal is heated to a certain temperature range. The advantages are that it can eliminate internal stress, avoid work hardening, increase the plasticity of the material, reduce the deformation resistance, and reduce the power consumption of the equipment.
Die structure: A die is a tool that separates or deforms the sheet metal. It consists of an upper die and a lower die. The die handle of the upper die is fixed on the slide block of the punch press and moves up and down with the slide block, and the lower die is fixed on the workbench of the punch press.
The punch and the die are the working parts in the die that deform or separate the blank, and are respectively fixed on the upper and lower template by pressing plates. The upper and lower die plates are respectively equipped with guide sleeves and guide posts to guide the alignment of the punch and the die. The guide plate and the positioning pin are used to control the feeding direction and feeding length of the blank, respectively. The function of the stripper is to release the workpiece or blank from the punch after punching.
Stamping die is an indispensable die in stamping production. Punching dies can be basically divided into three types: simple dies, continuous dies and composite dies.
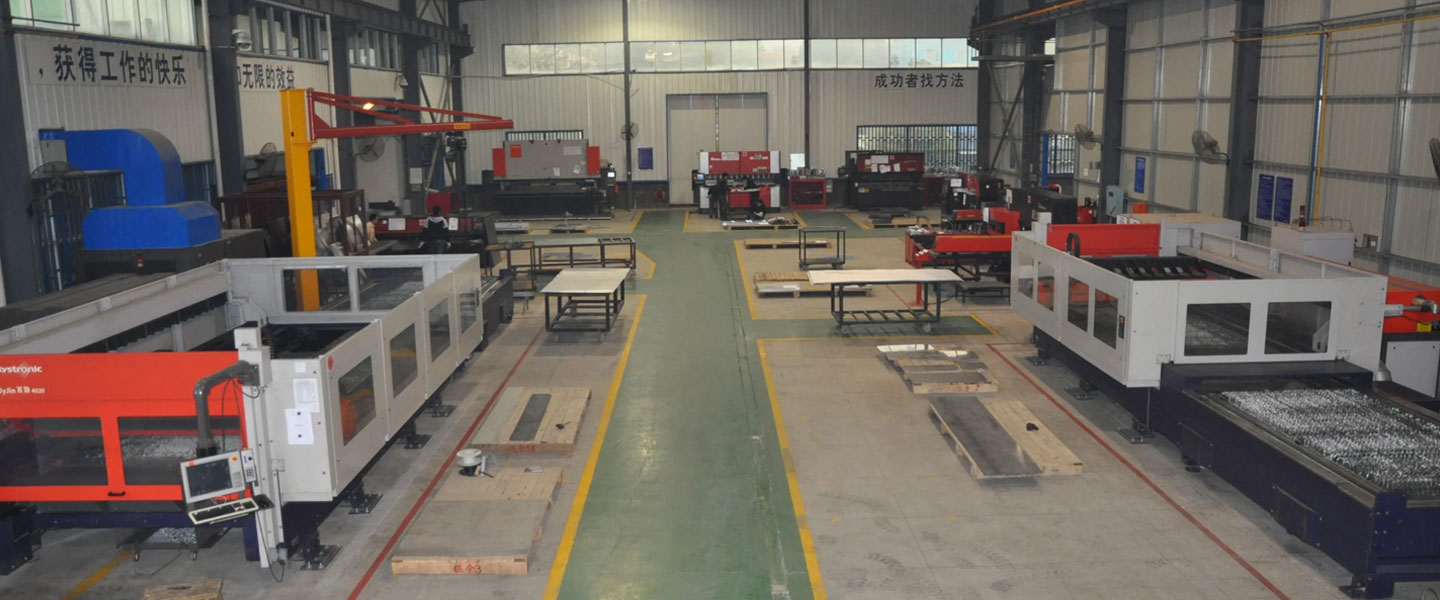
Pintejin Sheet Metal shop offers a cost-effective solution for a wide range of industries with our custom metal stamping and custom sheet metal fabrication capabilities. Our stampnig operations include a variety of sheet-metal forming manufacturing processes, such as punching, blanking, embossing, bending, flanging, and coining. Our professional, experienced and well-trained engineers can execute the complex metal stamping operations with precision and accuracy.
No matter what your metal fabrication needs are, Pintejin can offer the right solution: from single sheet metal part or sub-assembly of stamped metal parts to turnkey solutions for mechanical and electrical assemblies. We have the technology, equipment and the experience to fabricate customised metal products from aluminium sheet metal fabrication, steel, zinc plated steel, stainless steel sheet metal fabrication, brass and copper. Designs that require CNC machining of surfaces or components can be accommodated. We can supply polished, galvanized, zinc coated or powder coated finishes for any sheet metal work or stamped metal components. Coupled with our accurate and reliable metal fabricating equipment, we guarantee precision and repeatability in custom sheet metal work. You’ll be taking advantage of the best sheet metal fabrication china can produce.