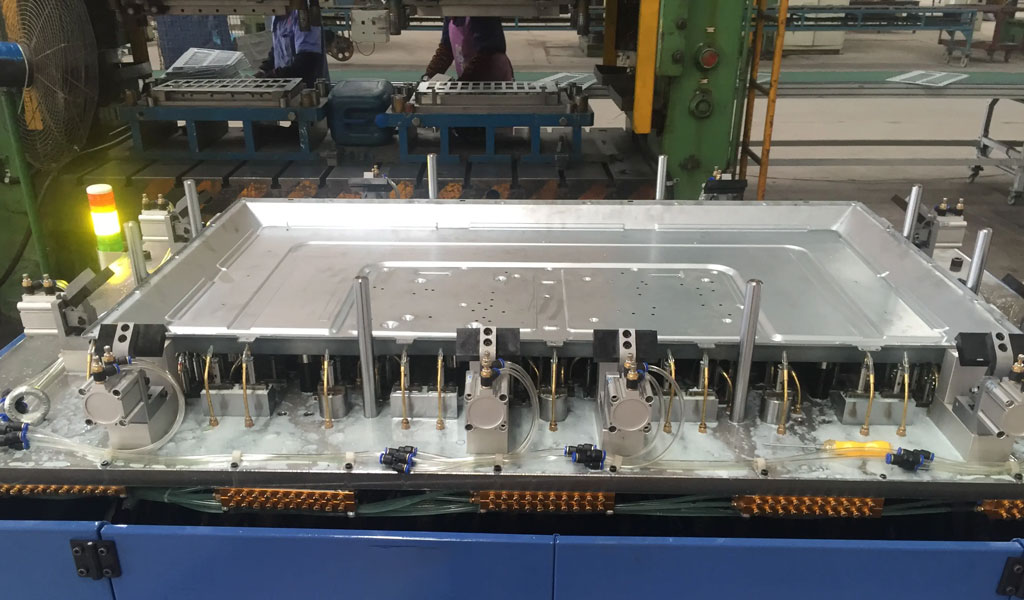
Sheet Metal Punching
Sheet Metal punching and blanking is to use the single-chip microcomputer on the cnc punching machine to input the fabrication program (size, fabrication path, fabrication tools, etc.) of the sheet metal parts in advance, so that the CNC punching machine can use various tools, through rich NC commands Various forms of punching, trimming, forming, etc. can be realized. CNC punching – generally cannot achieve punching and blanking with too complex shapes. Features: fast speed, saving mold. Flexible and convenient fabrication. Basically, it can meet the needs of sample blanking production.
Problems and requirements to pay attention to: thin material (t<0.6) is not easy to process, and the material is easily deformed; the fabrication range is limited by tools, clamping jaws, etc.; moderate hardness and toughness have good punching performance; hardness is too high It will increase the punching force, which will have a bad effect on the punch and accuracy; if the hardness is too low, the deformation will be serious during punching, and the accuracy will be greatly limited; high plasticity is good for forming, but not suitable for nibbling , Continuous punching is not suitable for punching and trimming; proper toughness is beneficial to punching, it can restrain the degree of deformation during punching; too high toughness will cause serious rebound after punching, but affect the accuracy.
CNC punching – generally suitable for punching low carbon steel, galvanized sheet, aluminum plate, copper plate, stainless steel plate below t=3mm with t=3. The plate and copper plate are 0.8~4.0, the low carbon steel plate is 0.8~3.5mm, and the stainless steel plate is 0.8~2.5mm. The deformation of the copper plate is large, and the CNC punching of the PC and PVC plates has large burrs and low precision.
The diameter and width of the tool used for stamping must be greater than the material thickness. For example, a tool with a φ1.5 cannot punch a material with a thickness of 1.6 mm.
Cold Die Punching And Blanking
For punching and blanking parts with large output and not too large size, in order to improve production efficiency, a special sheet metal stamping die is opened. – .Generally consists of punch and die. Concave molds generally include: press-in type, inlaid type, etc. Punch types are generally: round, replaceable; combined type; quick loading and unloading type, etc. The most common punching dies are: punching dies (mainly: open blanking die, closed blanking die, punching blanking compound die, open punching blanking continuous die, closed punching blanking continuous die) , bending die, calendering die.
Features: Because the punching and blanking can be basically completed in one time with a cold die, the efficiency is high, the consistency is good, and the cost is low. Therefore, for the structural parts with large output and not too large part size, the fabrication factory “generally opens the cold die for fabrication. In the structural design, it is necessary to consider the design according to the process characteristics of the open cold die fabrication.For example, the parts should not have sharp corners (except for It must be used outside), and it needs to be designed with rounded corners, which can improve the quality and life of the mold, and also make the workpiece beautiful, safe and durable; in order to meet the functional requirements, the structure and shape of the parts can be designed to be more complex.
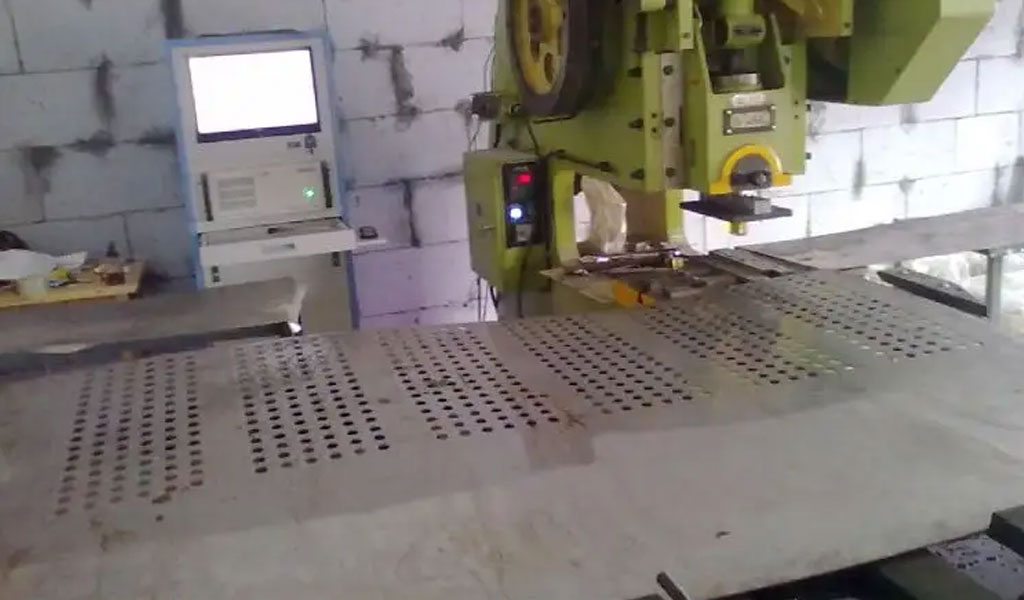
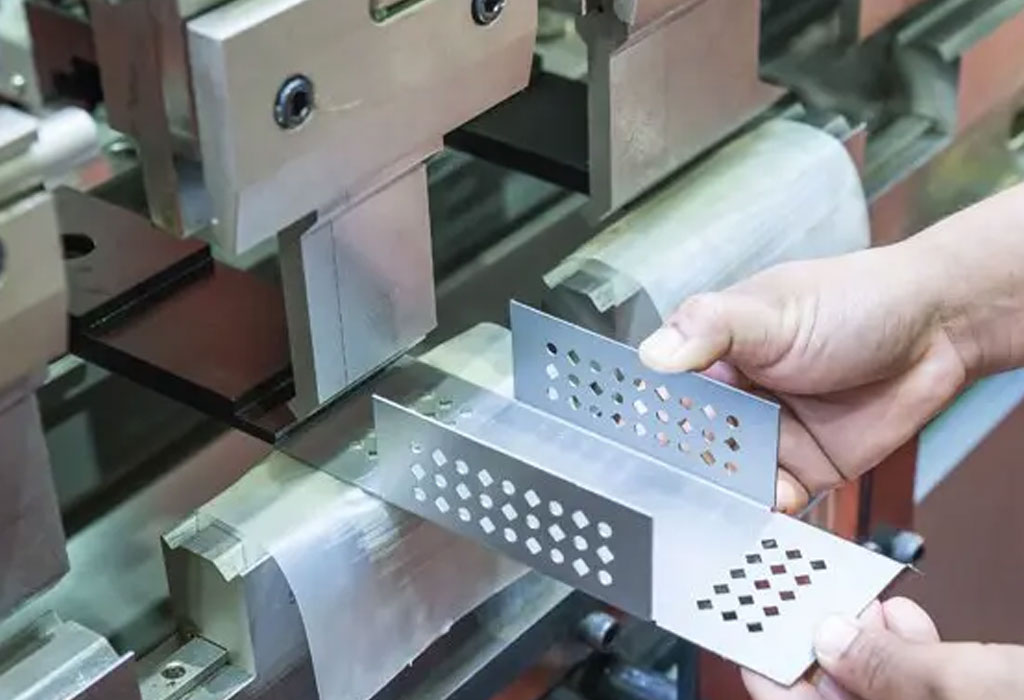
Dense Hole Punching
Dense hole punching can be regarded as a kind of CNC punching. For parts with a large number of dense holes, in order to improve the punching efficiency and accuracy, a punching die that can punch a large number of dense holes at one time is specially opened to process the workpiece. Such as: ventilation mesh panels, inlet and outlet air baffles, etc. See Figure 2.1.3-1. The shaded part in the figure is the dense hole die, and the dense hole of the part can be punched out quickly by the dense hole die. Compared with punching one by one, the efficiency is greatly improved.
Punching By Laser Cutting
Laser cutting is a non-contact cutting technology that uses electronic discharge as the energy supply, and uses a mirror group to focus to generate a laser beam as a heat source. This high-density light energy is used to achieve punching and blanking of sheet metal parts.
Features: Diversified cutting shapes, faster cutting speed than wire cutting, small heat-affected zone, no material deformation, fine incision, high precision and quality, low noise, no tool wear, no need to consider the hardness of the cutting material, can be processed large, Parts with complex shapes and difficult to machine by other methods. However, its cost is high, and at the same time, it will damage the support table of the workpiece, and the cutting surface is easy to deposit oxide film, which is difficult to handle. – -General Only suitable for single piece and small batch fabrication.
Problems and requirements to pay attention to: generally only used for steel plates. Aluminum plate and copper plate – generally cannot be used, because the heat transfer of the material is too fast, causing melting around the incision, and the machining accuracy and quality cannot be guaranteed. The end face of laser cutting has a layer of oxide skin, which cannot be removed by pickling, and the cutting end face with special requirements should be polished;
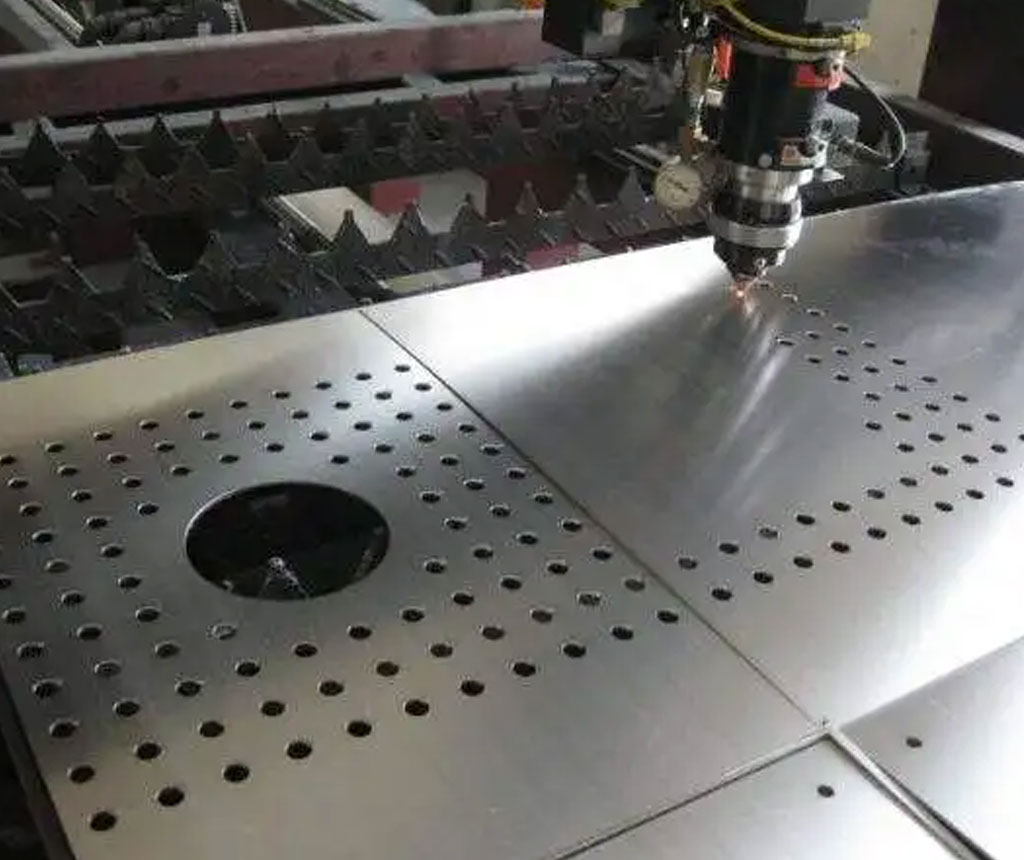
Punching By Wire Cutting
Wire Cutting is fabrication method that uses the workpiece and the electrode wire (molybdenum wire, copper wire) as one pole, and maintains a certain distance, forms a spark gap when there is a high enough voltage, and performs electro-erosion cutting on the workpiece. carried away by the working fluid.
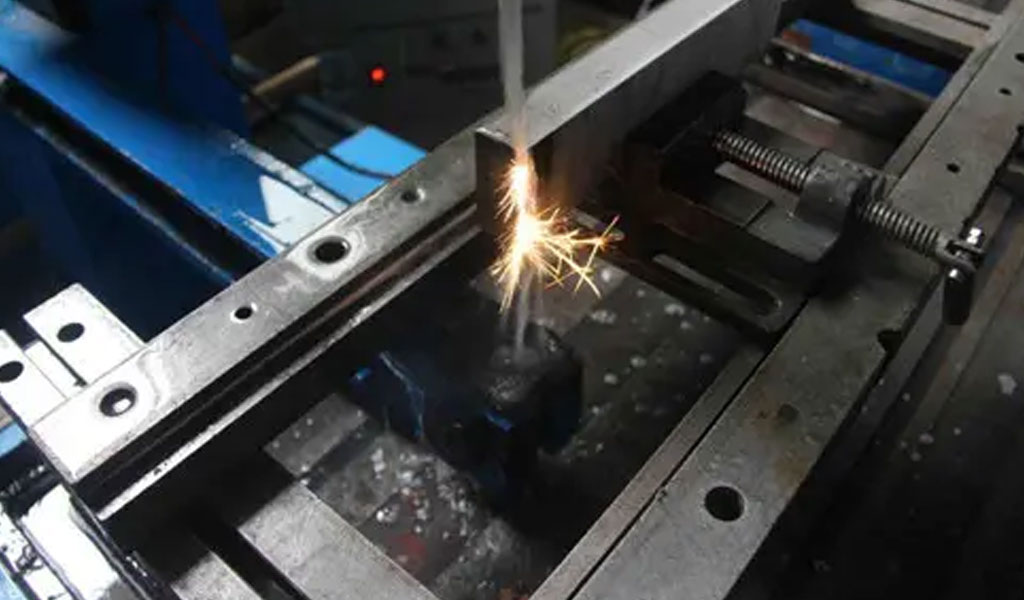
Features: High-end machining accuracy, but low-speed machining speed, high cost, and will change the surface properties of the material. Generally used for mold manufacturing, not used for fabrication production parts.
The square holes of some veneer profiles have no rounded corners and cannot be milled, and because aluminum alloys cannot be cut by laser, if there is no punching space, they cannot be punched, and only wire cutting can be used. The speed is very slow and the efficiency is very low, which cannot be adapted to mass production. , the design should avoid this.
The Characteristics Comparison Of Three Common Punching And Blanking Methods
Laser Cutting | CNC Punching (Including Dense Hole Punching) | Cold Die | |
---|---|---|---|
Machinable Material | Steel Plate | Steel Plate, Copper Plate, Aluminum Plate | Steel Plate, Copper Plate, Aluminum Plate |
Machinable Material Thickness Dli | 1mm ~8mm | 0.6mm~ 3mm | Generally Less Than 4mm |
Minimum Size For Machining (Ordinary Cold Rolled Steel Sheet) | Minimum Slit О.2mm Minimum Circle 0.7mm | Punching Round Hole 0 Lan t Square Hole Small Edge W Ramie L Long Groove Width W Ramie t | Punching Round Hole 0 blue t Square Hole Small Edge W t Long Groove Width W 2t |
Hole-To-Hole, Hole-To- Edge Minimum Distance | ≥ t | ≥ t | ≥ 1t |
Hole-To-Hole, Hole-To-Edge Preferred Distance | ≤ 1.5t | ≥ 1.5t | ≥ 1.5t |
General Machining Accuracy | ± 0.1mm | ± 0.1mm | ± 0.1mm |
Fabrication range | |||
Appearance | The Outer Edge Is Smooth, And There Is A Layer Of Oxide Skin On The Cut End Face | Large Burrs With Burrs | Small Amount Of Burrs |
Curve Effect | Smooth, Variable Shape | The Burrs Are Large And The Shape Is Standardized; | Smooth, Variable Shape |
Fabrication Speed | Cut Outer Circle Fast | Fast punching | Poe Kuai |
Fabrication Text | Etched, Shallower, Size Not Limited | Stamping Four-Shaped Characters, The Symbols Are Darker; The Size Is Limited By The Mold | Stamping, Called Pictograph, Symbol, Deeper; Size Limited By Die |
Take Shape | Cannot | Concave Points, Sinking Holes, Small Stretches, etc. | More Complex Shapes Can Be Realized |
Fabrication Fee | Higher | Low | Low |