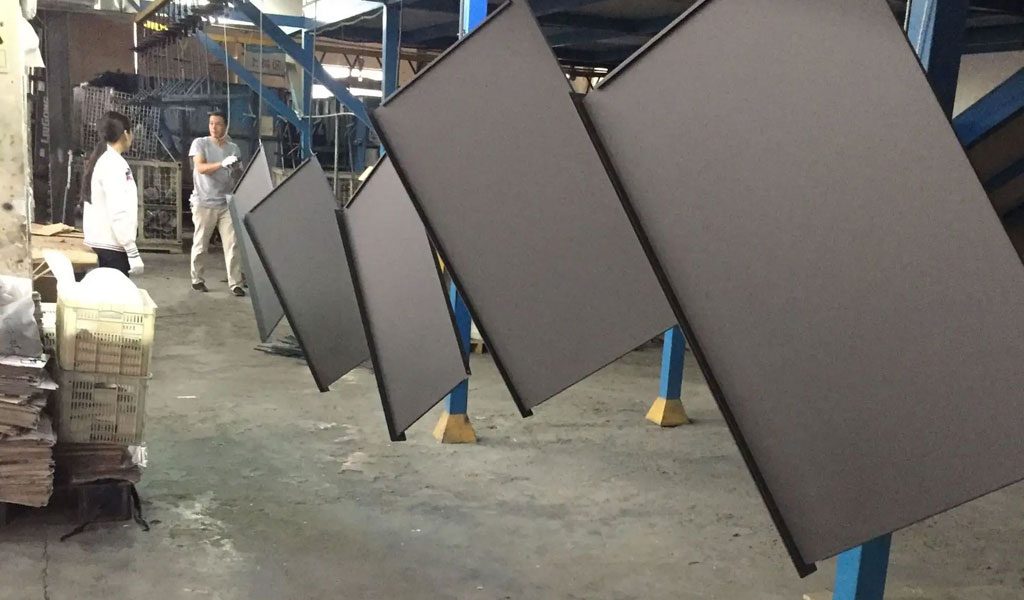
Sheet Metal Metal Finishing Service
Change the morphology, chemical composition and organizational structure of the product surface finishing and near-surface area in the most economical and effective way, effectively improve and improve the decorative performance, corrosion resistance and wear resistance of the product, and prolong the service life of the product. Common metal finishing : electroplating, electroless plating, conversion coating technology, physical vapor deposition, chemical vapor deposition, thermal spraying, hot dipping, sandblasting, chemical conversion, anodizing, painting, etc.;
Metal Finishing technology can also impart surface Various optical, electromagnetic, thermal, sonochemical and functional conversion properties.
- Various light surface technologies: mirrors; anti-reflective
- Various electrical surface technologies: insulating silver, gold, copper; conductive plastic protection
- Various magnetic surface technologies: Stealth technology (emphasis)
- Thermal surface technology: infrared, infrared absorption, heat protection;
- Acoustic Surface Technology: Anti-Sonar
- Chemical: Galvanized steel
Types of surface treatment Surface treatment can be divided into: protective surface treatment, such as electroplating, oxidation (chemical oxidation, electrochemical oxidation), decorative surface treatment (such as painting, functional surface treatment, total In other words, there is no clear dividing line, and its main purpose is to prolong the service life of the product and to save and utilize resources to the greatest extent.
Common Surface Treatments Methods For Sheet Metal
1.Electroplating For Sheet Metal Parts
The technology of depositing well-adhered metal coatings with different performance matrix materials on mechanical products by electrolysis.The electroplating layer is more uniform than the hot-dip layer, and is generally thinner, ranging from several microns to tens of microns. Through electroplating, decorative protective and various functional surface layers can be obtained on mechanical products, and parts that are worn and machined incorrectly can also be repaired.
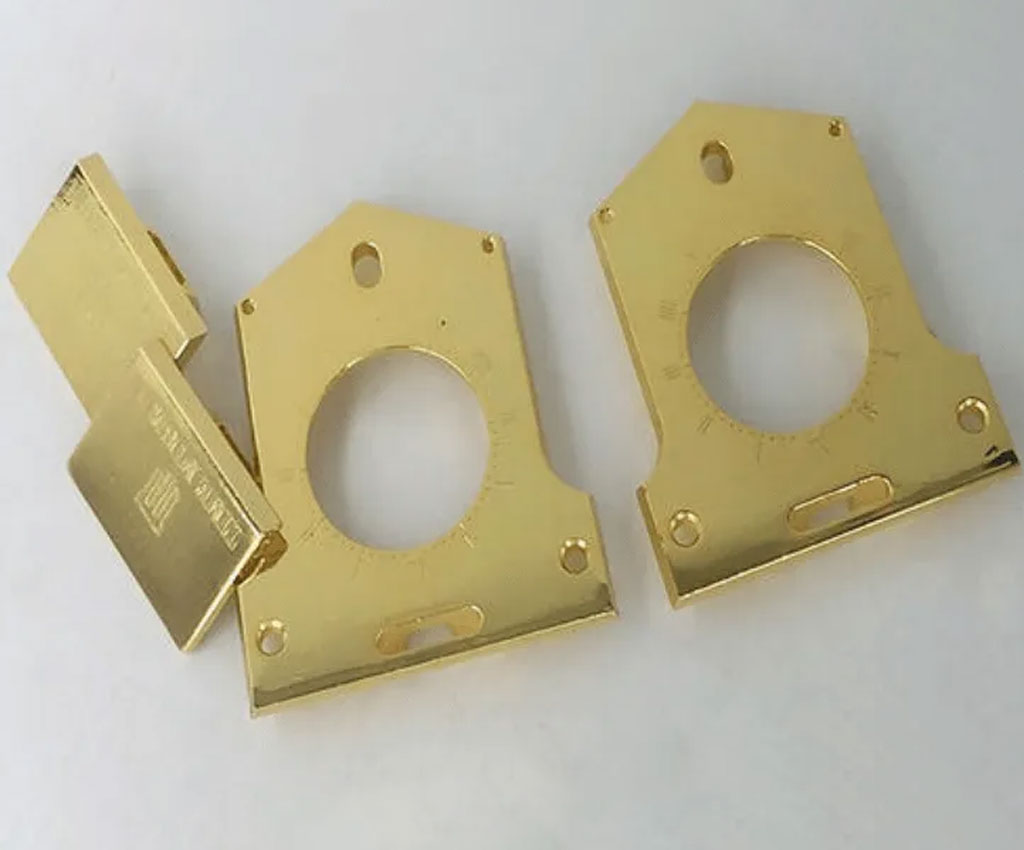
In addition, there are different functions according to various electroplating needs. An example is as follows:
- Copper Plating: used as a primer to improve the adhesion and corrosion resistance of the electroplating layer.
- Nickel Plating: used as a primer or as an appearance to improve corrosion resistance and wear resistance (among them, chemical nickel is more wear-resistant than chrome plating in modern technology).
- Gold Plating: Improve conductive contact resistance and improve signal transmission.
- Palladium-Nickel Plating: Improves conductive contact resistance, improves signal transmission, and has higher wear resistance than gold.
- Tin And Lead Plating: improve the welding ability, and will soon be replaced by other substitutes (because most of the lead is now plated with bright tin and matte tin)
2.Dusting Or Sandblasting For Sheet Metal Parts
- A thicker coating can be obtained by one coating. For example, a coating of 100-300 μm needs to be coated 4 to 6 times with a common solvent coating, while this thickness can be achieved with a powder coating at one time. . The corrosion resistance of the coating is very good. (We recommend that you pay attention to the “Mechanical Engineer” public account, and master the knowledge of dry goods and industry information as soon as possible)
- The powder coating contains no solvent and no pollution of the three wastes, which improves the labor and hygiene conditions.
- New technology such as powder electrostatic spraying is adopted, which has high efficiency and is suitable for automatic assembly line painting; the powder utilization rate is high and can be recycled.
- In addition to thermosetting epoxy, polyester, acrylic, there are a large number of thermoplastic grease-resistant can be used as powder coatings, such as polyethylene, polypropylene, polystyrene, fluorinated polyether, nylon, polycarbonate and various Fluorine resin, etc.
3.Electrophoresis For Sheet Metal Parts
Electrophoretic paint film has the advantages of full, uniform, flat and smooth coating. The hardness, adhesion, corrosion resistance, impact performance and penetration performance of electrophoretic paint film are obviously better than other coating processes.Detailed features:
- The use of water-soluble paint and water as the dissolving medium saves a lot of organic solvents, greatly reduces air pollution and environmental hazards, is safe and hygienic, and avoids the hidden danger of fire;
- The coating efficiency is high, the coating loss is small, and the utilization rate of the coating can reach 90% to 95%;
- The thickness of the coating film is uniform, the adhesion is strong, and the coating quality is good. All parts of the workpiece, such as inner layers, depressions, welds, etc., can obtain a uniform and smooth paint film, which solves the problem of other coating methods for complex shape workpieces. coating problems;
- High production efficiency, automatic continuous production can be realized in construction, which greatly improves labor efficiency;
- The equipment is complex, the investment cost is high, the power consumption is large, the temperature required for drying and curing is high, the management of paint and coating is complex, the construction conditions are strict, and wastewater treatment is required;
- Only water-soluble paint can be used, and the color cannot be changed during the coating process, and the stability of the paint after being stored for a long time is difficult to control.
- The electrophoretic coating equipment is complex and the technology content is high, which is suitable for the production of fixed color.
4.Dip For Sheet Metal Parts
Dip technology can provide a flexible protection for rigid objects, with insulation, pressure resistance, flame retardant, temperature resistance, waterproof, dustproof, anti-static and other characteristics.
Why Do We Need Surface Treatment In Sheet Metal Fabrication
- The materials used in sheet metal fabrication are mostly cold-rolled sheets, hot-rolled sheets, electrolytic sheets, white iron, stainless steel, aluminum alloy sheets and profiles, copper materials, etc. After the oxygen is fully contacted, an electrochemical reaction will occur, which will cause the surface of the material to corrode, and at the same time, the potential difference will form a galvanic cell, resulting in contact corrosion. In order to avoid the corrosion of the material between the various fabrication steps and the finished product during the storage and use of the sheet metal fabrication, the product is repaired or scrapped by the surface corrosion of the material in the production, so as to save resources and production costs as much as possible.
- When various materials are converted into commodities through sheet metal fabrication, in order to meet the needs of customers and the visual beauty of the commodities, various surface treatments are applied to the appearance of the products, such as electroplating, oxidation, etc.
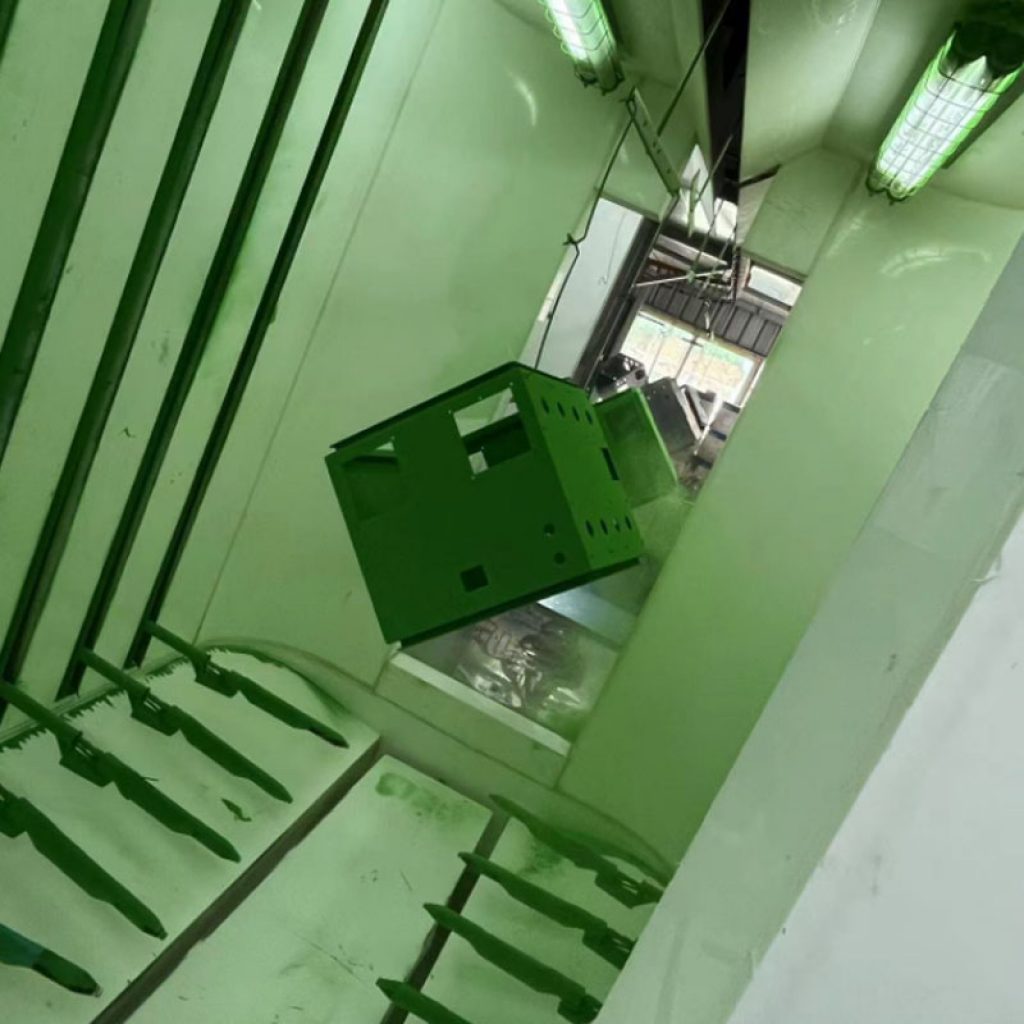
What Surface Treatments Are Usually Required For Aluminum Alloy Materials In The Sheet Metal Fabrication Industry?
In the sheet metal fabrication industry, aluminum alloy materials usually need the following surface treatments: colorless chemical oxidation, black chemical oxidation, golden yellow chemical oxidation, wire drawing colorless chemical oxidation, sandblasting colorless chemical oxidation, bright colorless chemical oxidation, Sandblasting bright anodizing, chemical oxidation coloring, coating after chemical oxidation (painting, powder spraying), in which the oxide layer has two types of conductive and insulating; hard, wear-resistant, etc.;
Common Surface Defects Summary Of Sheet Metal Parts
For sheet metal parts, the surface quality should be very important. Here, according to the accumulation of our own experience, we will briefly describe the various problems that are prone to occur.
- Concave and convex: the reasons for the stamping die and the stamping process lead to unevenness.
- Scratches: The parts are scratched due to other reasons, which may be caused by the parts, or may be caused by external reasons.
- Corrosion: The product is rusted due to improper protection, or because the shelf life is too long, or the material does not meet the requirements, or the anti-rust oil does not meet the requirements.
- Indentation: The defect caused by the repair or damage of the mold to the product.
- Wrinkling: wrinkles on the product.
- Deformation: The product is deformed, and most of the contact is caused by subsequent bumps, or the rebound of the material.
- Cracking: caused by the drawing process or stress concentration.
- Dislocation: The welding position is deviated during welding.
- Blocking hole: For the position with nut hole, the welding dislocation causes the nut hole to be blocked.
- Leaving the air: the coordination of the two parts is not ideal, and there is a gap in the middle.
- File marks: After the product surface is defective, it is repaired with a file, so that marks are left later.
- Polishing marks: traces left after the product is polished.
Welding defects: virtual welding, missing welding, welding deviation, welding penetration, welding slag, welding point depression, welding point distortion, welding point crack, welding point burr, welding point spacing.
- Welding: The two parts are not fused together. After being pulled apart by a destructive test, the fusion surface is too small or not fused. Usually caused by equipment parameters. When other parts of the welding equipment are in contact with the welding parts, it will cause a short circuit, resulting in false welding; caused by factors such as excessive current and voltage; there are gaps between the parts, resulting in tiny voids, etc.; voltage fluctuations also There will be virtual welding, the aging of the cable, the operating position, etc. are all related.
- Leakage welding: For sheet metal parts, it is normal to weld multiple points on it, so there are often cases of missing welding points. Standardized work should be performed. (We recommend that you pay attention to the “Mechanical Engineer” public account, and master the knowledge of dry goods and industry information as soon as possible)
- Welding deviation: The position of the solder joint is not correct and deviates from the predetermined position.
- Welding penetration: The reason of equipment parameters (such as excessive current) or the distance between the two parts during welding is large, resulting in current breakdown; oil or rust or other things between the welded parts can cause breakdown.
- Welding slag: sparks splash during welding, which is formed by
- Solder joint depression: After spot welding, the solder joint is uneven, forming a concave point.
- Distortion of solder joints: The solder joints are uneven and deformed after spot welding. The defect is formed only when the contact surface of the welding gun is not perpendicular to the surface of the welding workpiece, and it is easy to occur at the edge welding point.
- Solder joint cracks: small cracks generated at the solder joints.
- Solder joint burrs: There are burrs at the solder joints, and the welding pliers need to be maintained. Excessive current will cause spatter; edge solder joints are prone to burrs; excessive pressure may also cause burrs; the welding posture should be accurate.
- Spacing of solder joints: the distance between solder joints and solder joints.