
Sheet Metal Bending
The working principle of sheet metal bending forming is to fix the upper and lower molds on the upper and lower worktables of the bending machine respectively, and use the servo motor to transmit the relative motion of the hydraulically driven worktable, combined with the shape of the upper and lower molds, thus Realize sheet metal bending and forming of sheet metal. with the addition of CNC function and into various angles, advanced sheet metal bending service improved fabrication accuracy and production efficiency are effectively.
The forming accuracy of the bending can reach 0.1mm per fold.Common bending forming: Usually, the forming that we can complete with a bending machine includes 90-degree bending, non-90-degree bending, dead edge (including a gap less than the thickness of the plate), level difference, etc.
Sheet Metal Bending Services Online – Large CNC Metal Bending Company In China
Pintejin is a trusted online bending services supplier that is able to provide custom sheet metal bending parts for your project with top quality and fast shipping. With decades of experience and expert capabilities, our sheet metal bending services can bending an extensive range of metal materials using Large rolling machine, absolute bending machine and other technologies. According to your requirements and applications, we’ll offer suggestions for the product design, suitable materials, and the most cost-effective methods for bending and manufacturing. Minimal cost, time and best quality are our purposes. Equipped with state-of-the-art facilities and measuring equipment in our factory, precision sheet metal fabrication now supply sheet metal bending parts for a number of business sectors and private individuals, catering both long and short production runs.
The Case & Products Of Sheet Metal Bending
Currently, our non-standard Sheet Metal Bending parts are exported to America, Canada, Australia, United Kingdom, Germany, France, Sout Africa, and many other countries all over the world. We are ISO9001-2015 registered and also certified by SGS.
Our custom Sheet Metal Bending service provides durable and affordable parts that meet your specifications for automotive, medical, aerospace, electronics, food, construction, security, marine, and more industries. Fast to send your inquiry or submit your drawings to get a free quote in the shortest time.Contact us or Email [email protected] to see how our people, equipment and tooling can bring the best quality for the best price for your custom Sheet Metal Bending project.
-
What are the repair methods for car body sheet metal damage?
-
How about the application of cold stamping process in automobile stamping parts?
-
The principles that need to be followed in the fabrication of precision metal automobile stamping parts?
-
What are the technical characteristics of high-speed precision stamping parts?
-
What are the advantages of the new automotive sheet metal process?
-
Application of Micro-Joint Processing Technology of CNC Punching Machine in Sheet Metal Manufacturing
The Types Of Sheet Metal Bending Moulds
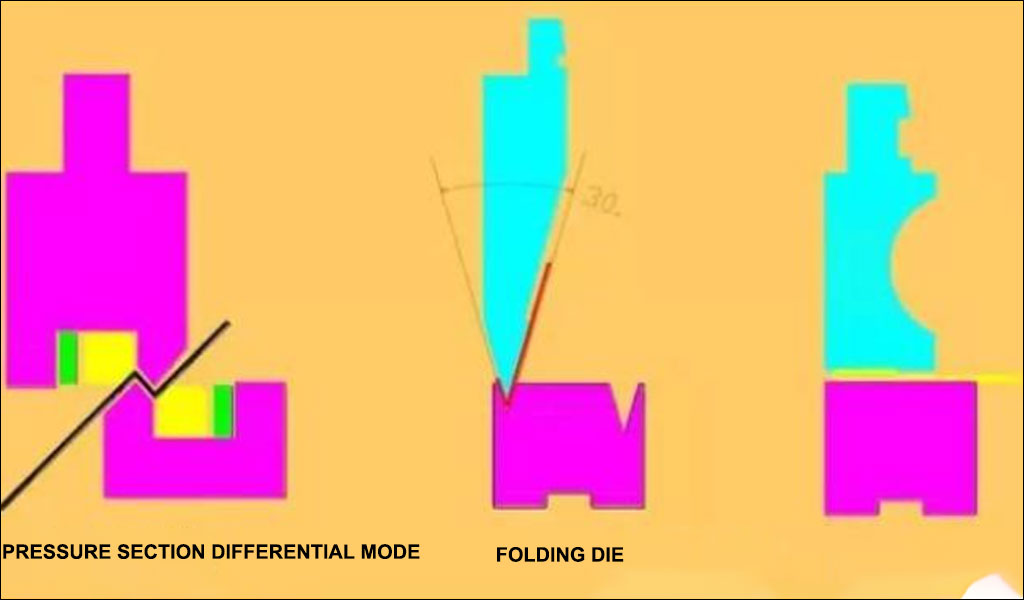
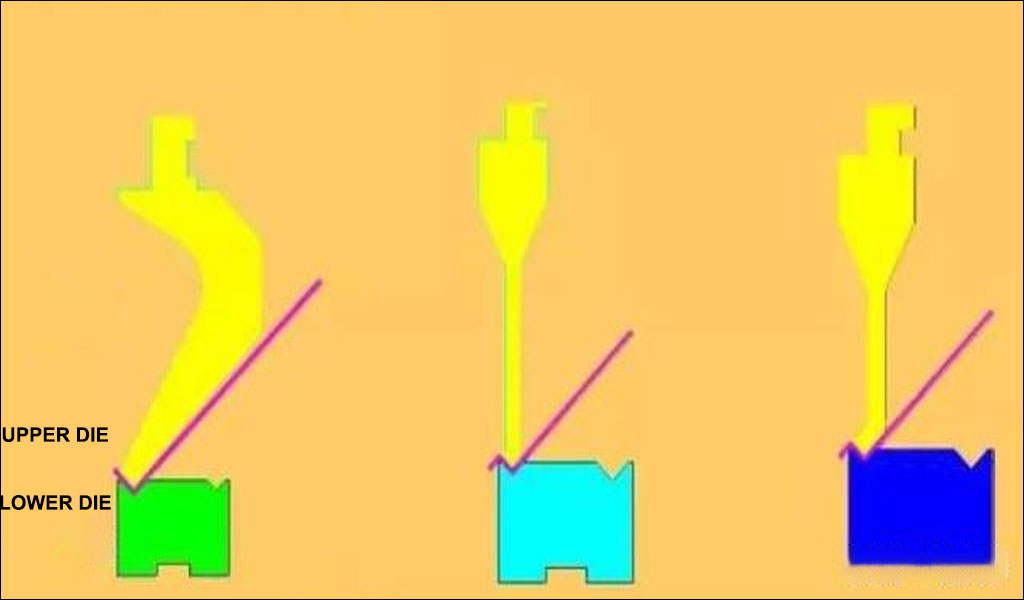
When bending two adjacent folded edges, if there is a hemming relationship between each other, a process hole (the diameter of the process hole is not less than the thickness of the plate) should be considered in the corner of the bending, and a reasonable gap (0.15 times the thickness of the plate) should be reserved. sheet thickness).
The minimum distance from the hole to the edge of the bending part. Usually, we take down 1/2+0.5 of the width of the die groove (as shown in the figure on the right). When designing sheet metal parts, try to avoid the occurrence of folded edges or hole spacing. When the edge distance is less than the size requirement
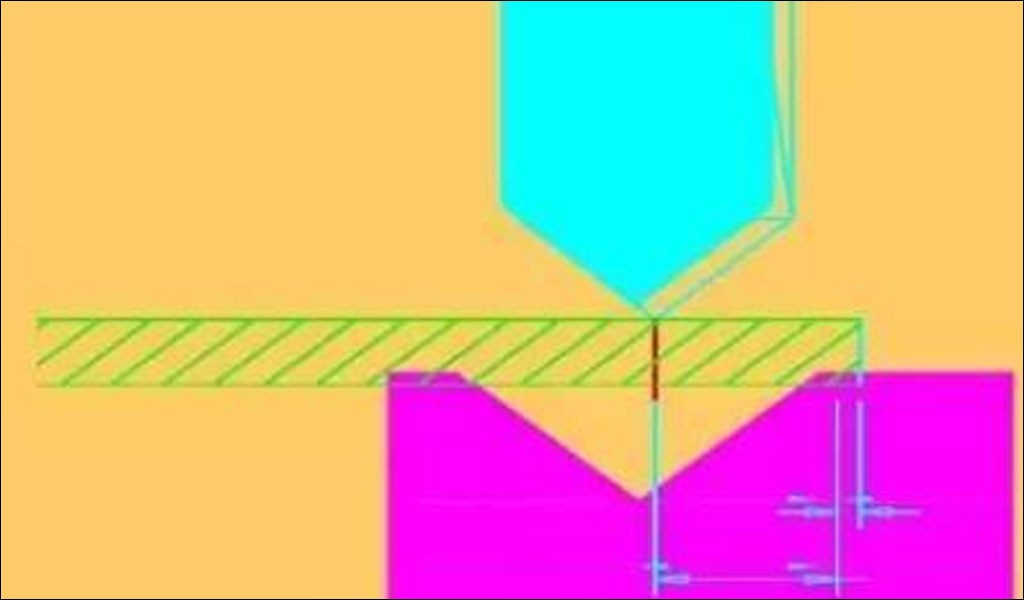
The width of the lower die groove is determined according to the plate thickness (T), as shown in the table:
Plate Tthickness T | 0.5-3 | 3.0-8 | 9-10 | 12 or more |
Slot Width | 6T | 8T | 10T | 12T |
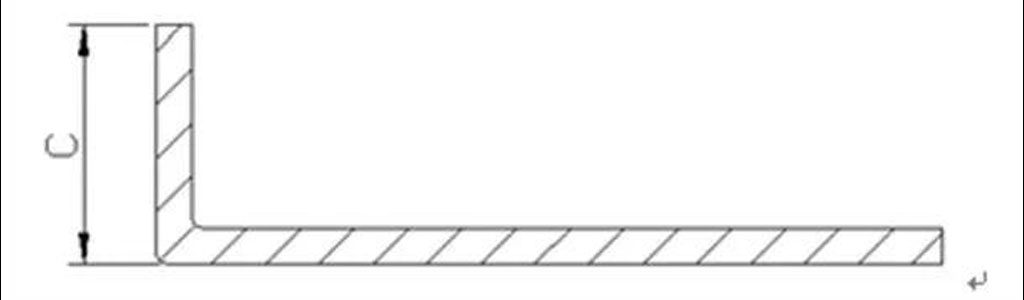
Sheet Metal Bending Design Requirement
Sheet Metal Bending is limited by the mold, and there are requirements for the minimum bending height. The specific requirements are shown in Table 1 in Figure 1:
Material Thickness | 0.8 | 1.0 | 1.2 | 1.5 | 2.0 | 2.5 | 3.0 | 4.0 | 5.0 | 8.0 |
Minimum Bending Height C | 5.5 | 6.0 | 6.5 | 7.5 | 8.0 | 12.0 | 12.0 | 17.0 | 19.0 | 55.0 |
The above analysis is based on the case where only one-knife bending is performed. For parts whose bending direction of the second knife is inconsistent with that of the first knife, the minimum bending height C as shown in the figure below, the height of C is (V groove/2+t+4) mm (V groove is the width of the bending die groove, t is the material thickness, unit: mm)
The Minimum V-groove Selected For Different Material Thicknesses In Cnc Die Bending
Material Thickness T(mm) | 0.5 | 0.6 | 0.8 | 1 | 1.2 | 1.5 | 2 | 2.5 | 2.75 | 3 | 4 | 5 |
Minimum V Groove Width (mm) | V4-V6 | V4-V6 | V6-V10 | V8-V10 | V10-V12 | V10-V12 | V10-V12 | V18 | V25 | V25 | V25 | V25 |
Punching dies and blanking dies require a reasonable gap between the punch and the die, and the gap is generally 5% to 10% of the plate thickness. Using a punching die with a diameter of 50mm to produce a blanking part with a diameter of 50mm cannot guarantee the accuracy of the stamping part, because the size of the hole on the workpiece depends on the size of the punch, and the outer dimension depends on the size of the die.
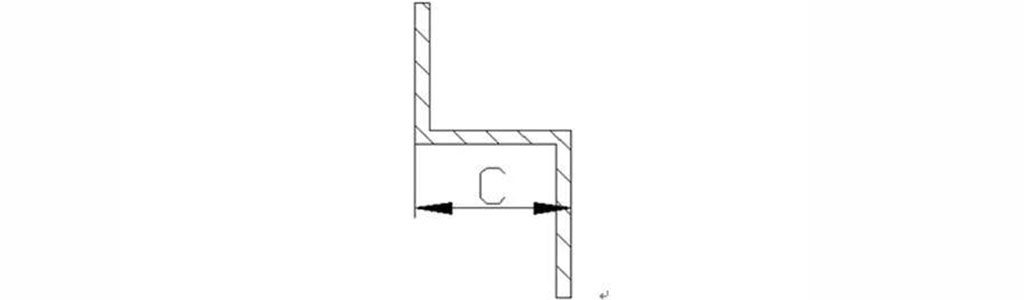
Schematic Diagram Of The Second Knife Bending
For the concave and U-shaped bending parts shown in Figure 2, the angle a should generally be followed by not more than 45°. The bending shape shown in Figure 3 is suitable for parts with material thickness ≤ 2 mm, and the size requirements are shown in Table 2.
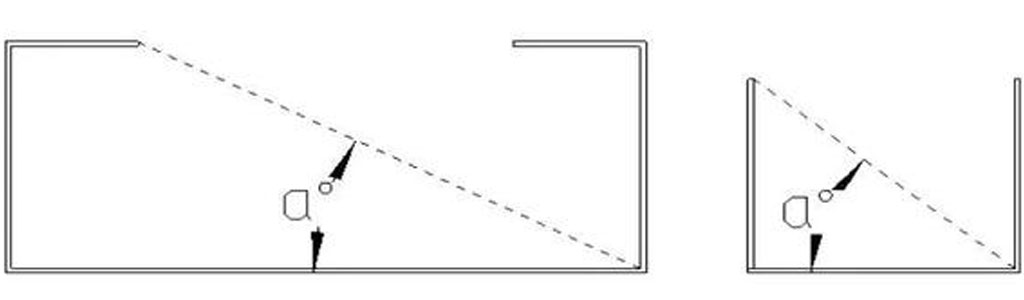
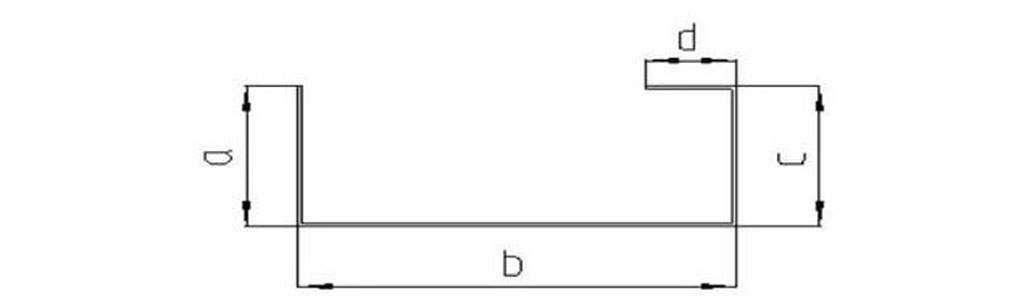
Size | a | b | c | d |
Size Requirements | 0-50 | 10-50 | 0-50 | 0-50 |
The CNC bending of sheet metal parts with a thickness of t=8.0 is limited by the mold, and there are requirements for the minimum bending height and bending fillet. The requirements are as follows (Table 3):
Minimum Bending Height (Packing Thickness) Hmin | Hmin=55mm |
Bend Fillet R | R= 13mm |