- Sheet Metal Material: Copper Sheet
- Sheet Thickness: 1-3 (mm)
- Fabrication Size/Length*Width*Height: Custom
- Molded Parts: Plate
- Blanking Method: Custom
- Tolerance: 0.1mm
- Surface Treatment: paint
- Surface Roughness: 0.1
- Annual Remaining Fabrication Capacity: 1,000,000
- Proofing Cycle: 4-7 days
- Rapid Prototyping Cycle: 4-7 days
- CE & ISO&ITAF:Pass
- Quality Control:CMM And More
- Drawing format:3D/CAD/DWG//STEP/PDF/etc.,
OEM Copper Communication Equipment Enclosure Manufacturer
Heat and corrosion resistant fabrication services for OEM Copper Communication Equipment Enclosure and other industries. Capable of handling sheets in minimum 1/16 in. sizes. Processes include rolling, welding, bending, stamping and press brake forming. Provides metallurgical services such as non-destructive testing, weld certification and final inspection services. Meets API, ASME, AWS, ASTM and DOT standards.
The Advantages Of Pintejin Custom Sheet Metal Fabrication Service
Sheet metal fabrication services for mild steel, high strength low alloy (HSLA) steel, cold/hot rolled steel, galvanized steel, stainless steel, aluminum, copper and brass. Various capabilities include contract manufacturing, edge rolling, forming, roll bending and welding. Finishing and secondary services such as hardware installation, tapping, deburring, cleaning, heat treating, plating, anodizing and painting available. Prototype and low to high volume production runs offered.
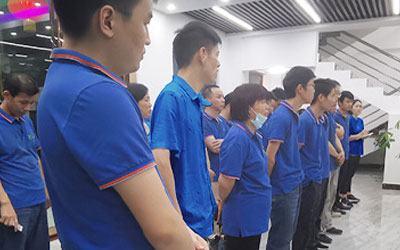
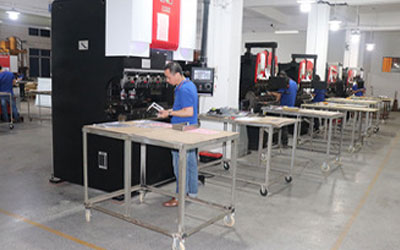
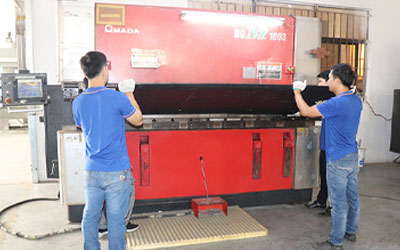
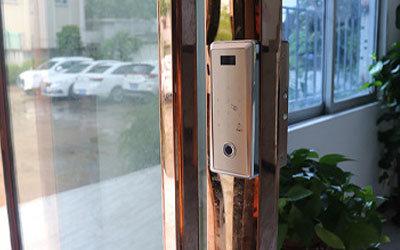
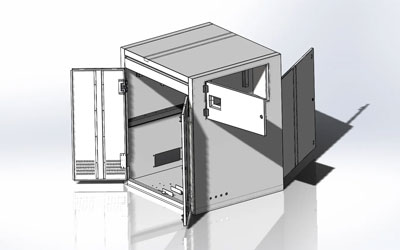
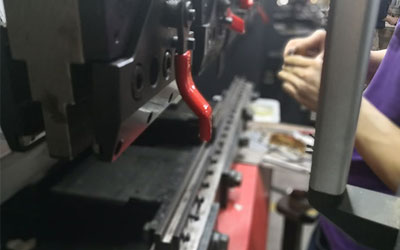
Points Sheet Metal Customers Should Know When Designing Drawings
Design Considerations for Sheet Metal Fabrication:
- Wall Thickness: Uniform thickness is very important for any geometry. Geometries with more than one wall thickness will require sheet metals of different thicknesses. Therefore, the alignment and orientation of parts may be inaccurate or take time.
- Bend Radii: It is important to keep the inside bend radius of sheet metal at least equal to its thickness. This will help to avoid distortions and fractions in the final parts. Maintaining the bend radii consistently across the part ensures cost-effectiveness and good orientation.
- Bend Allowance and Deduction: Bend allowance is the material needed to be added to the actual lengths of the parts to help develop a flat pattern. Bend deduction is the material needed to be removed from the length of flanges to help get a flat pattern.
- K Factor: K factor is the sheet metal process is the ratio of neutral axis to material thickness. This value changes with respect to the various physical properties and thickness of materials used.
- Holes and Slots Orientation: These factors are also very important. Holes and slots diameter should at least be as large as the thickness of the sheet metal. Also, holes should be reasonably spaced. They should never be too close to the edge of the material.
Currently, our non-standard sheet metal fabrication parts are exported to America, Canada, Australia, United Kingdom, Germany, France, Sout Africa, and many other countries all over the world. We are ISO9001-2015 registered and also certified by SGS.
Our custom sheet metal fabrication service provides durable and affordable parts that meet your specifications for automotive, medical, aerospace, electronics, food, construction, security, marine, and more industries. Fast to send your inquiry or submit your drawings to get a free quote in the shortest time.Contact us or Email [email protected] to see how our people, equipment and tooling can bring the best quality for the best price for your custom sheet metal fabrication project.